MODULA WMS
Warehouse Management System
Modula WMS software is a complete inventory management software ideal for traditional storage systems (manual racking areas) and automated storage systems. Modula WMS software can be used as the perfect complement for managing Modula vertical warehouses or as a standalone software tool for managing traditional warehouses (manual areas).
Modula WMS allows real-time warehouse management via a PC interface.
All that’s needed is a PC to act as the warehouse server and a certain number of client PC’s, depending on requirements.
Modula WMS installs the free Express version of SQL Server which does not require any licences. To use one of the more complete versions of the database engine, the client is responsible for obtaining the licenses as required. In either case the SQL Server database instance must be for the exclusive use of Modula WMS.
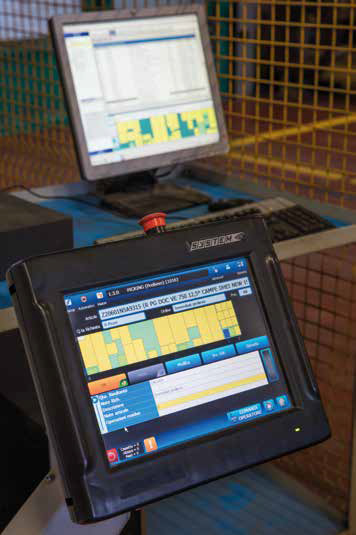
Software architecture
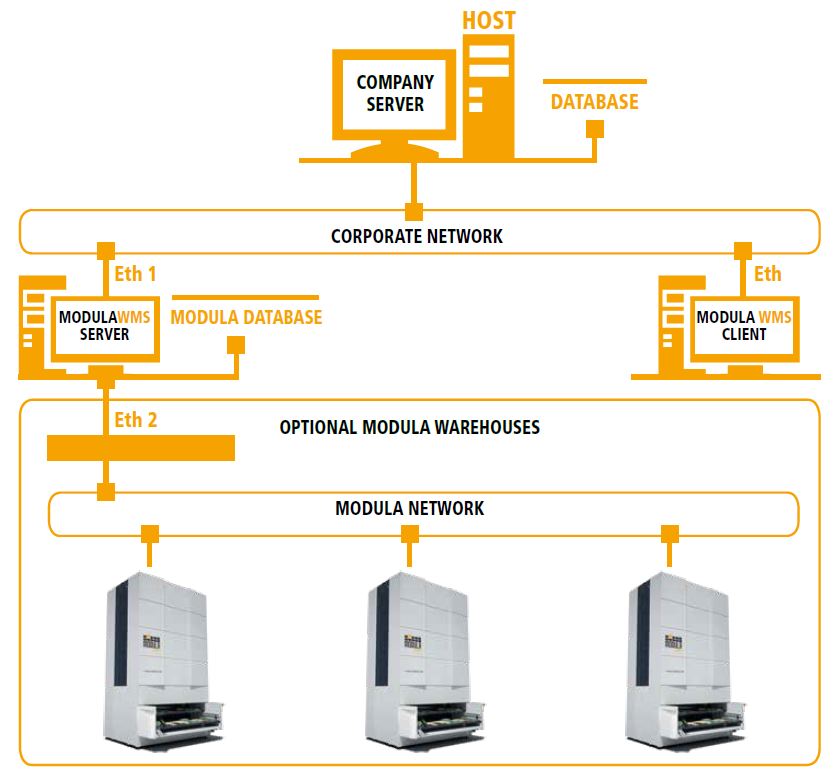
Advantages of using WMS

- 1. OPTIMISATION
- Static or dynamic management of locations without any inventory or warehouse redundancy.

- 2. ERP INTEGRATION
- Easy integration with ERP (SAP, Oracle, Microsoft, etc.), MRP or other company applications, providing precise and continuous exchange of information between these systems and Modula WMS.

- 3. SAVES TIME
- Traceability of materials and guided execution of loading and unloading to allow rapid order dispatch.

- 4. CONFIGURABILITY
- Can be customised and adapted to current management flows without impacting the company's organisation.

- 5. CONTROL AND EFFICIENCY
-
Maximum control over processes via:
• automation of repetitive procedures
• rationalisation of movements and routes
• elimination of errors
• reduced paperwork

- 6. SIMPLE TO USE
- Operating procedures have been designed to guarantee immediate and easy use, even by non-specialist personnel.
If your company doesn’t have a WMS
MODULA
WMS BASE
Modula WMS Base is considered our entry level package and is bundled with a Modula purchase; it is suitable for the management of one or more warehouses. This package can manage a maximum of 3 users (i.e. 3 PCs) and 2 clients.
This package supports:
- Item management.
- Warehouse locations management using a graphical tool.
- Materials handling management through picking/refilling orders.
- Materials handling management through immediate requests.
- User management with three hierarchical access levels.
- Management of physical warehouse inventories.
- Manual import/export data exchange system with the client’s ERP of fixed format ASCII files.
- Advanced security management with restricted access to specific item codes and trays based on user’s role.
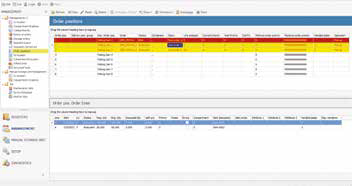
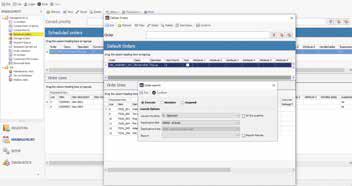
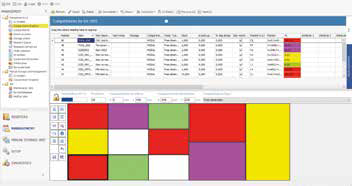
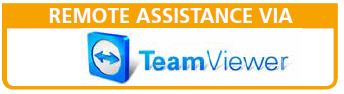
MODULA
WMS PREMIUM
The most complete package for warehouse management. Provides all the functionalities of the BASE package, plus many others.
What does WMS Premium do?
- Automatic item-compartment allocation and dynamic location management.
- Lot and serial number management.
- Full management with custom tracking of automatic import/export in ASCII, ODBC, Excel and XML file formats.
- Material status management.
- Pack type management.
- Expiration date management.
- Advanced user management; configuration of enabled procedures for each individual user.
- Material management by FIFO (First Input First Output) or by sub-code priority (e.g. picking can be performed giving priority to the lowest and therefore the oldest code).
- Justification management for immediate requests.
STATISTICAL ANALYSIS AND CUSTOM REPORTS
- Full management of warehouse statistics.
- Customization of print reports via print management tool.
- Customization of printed label layout using dedicated tools.
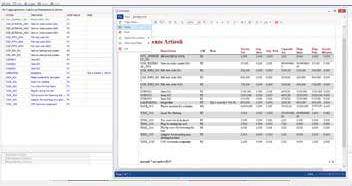
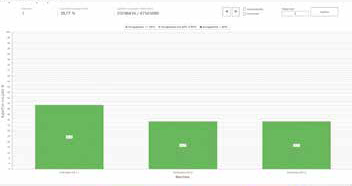
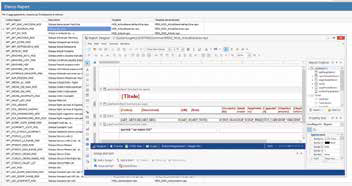
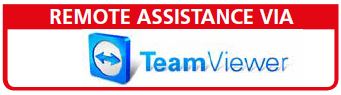
Your Modula systems under control
A Modula warehouse can be fitted with Modula Cloud. This control and diagnostics system allows you to access information about your warehouse remotely. Entirely designed to improve the performance of warehouses and to control all operations, Modula Cloud is a valuable source of information for managing activities such as error signalling, technical assistance, maintenance and spare parts ordering.
Modula Cloud operates using WMS software, which receives the information from the warehouse and transfers it to the Cloud and loads it onto a dedicated website accessible via a URL. In this way, each user will be able to view all their machines including with Google geolocation.
Modula Cloud monitors:
- Warehouse operations.
- Malfunction lights and alarms.
- Historic archive of blocks and errors.
- Number of tasks per day or per period.
- Errors generated by operators.
- Maintenance count downs.
- Energy consumption, tray weights and unit heights.
Vertical warehouses have a device that can receive input “warning” signals when the machine experiences malfunctions, to notify, in real time, the customer who has access to the platform, and Modula’s technical assistance who can then intervene providing appropriate support and preventive aintenance.
Given these warning signals, Modula’s electromechanical department can intervene remotely to reset the machine in real time. They just need the operator to confirm via the console using a simple wizard menu.
Like any data collection tool, it is extremely valuable for monitoring and improving warehouse performance, reducing intervention times, and having control of the entire system with one click.
The other added value is having the data in the Cloud, accessible from anywhere with dedicated logins.
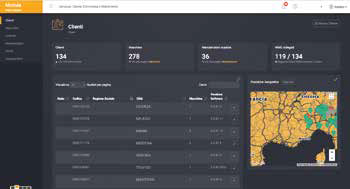
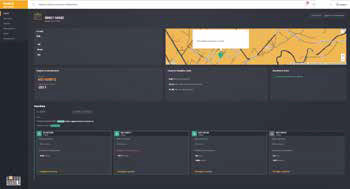
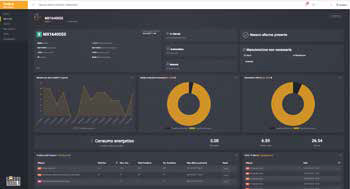